Navigating the Globe of Fasteners and Machining: Methods for Accuracy and Speed
In the complex world of fasteners and machining, the pursuit for precision and rate is a perpetual difficulty that requires meticulous focus to detail and critical planning. From understanding the diverse variety of fastener kinds to selecting optimum products that can hold up against strenuous demands, each step in the procedure plays a pivotal role in attaining the desired end result.
Understanding Fastener Kind
When picking bolts for a job, understanding the various kinds offered is essential for ensuring optimal efficiency and reliability. Screws are utilized with nuts to hold products with each other, while screws are flexible fasteners that can be used with or without a nut, depending on the application. Washing machines are necessary for dispersing the lots of the bolt and stopping damage to the material being fastened.
Picking the Right Products
Recognizing the value of selecting the best materials is vital in making certain the optimal performance and integrity of the chosen fastener types reviewed formerly. When it pertains to bolts and machining applications, the product option plays an important duty in identifying the overall stamina, resilience, deterioration resistance, and compatibility with the designated environment. Different products offer varying residential or commercial properties that can significantly affect the efficiency of the fasteners.
Usual products used for bolts consist of steel, stainless steel, brass, titanium, and aluminum, each having its special staminas and weak points. Steel is renowned for its high stamina and toughness, making it ideal for a vast variety of applications. Selecting the right product entails thinking about elements such as toughness demands, ecological conditions, and budget restraints to make certain the wanted efficiency and longevity of the bolts.
Precision Machining Techniques
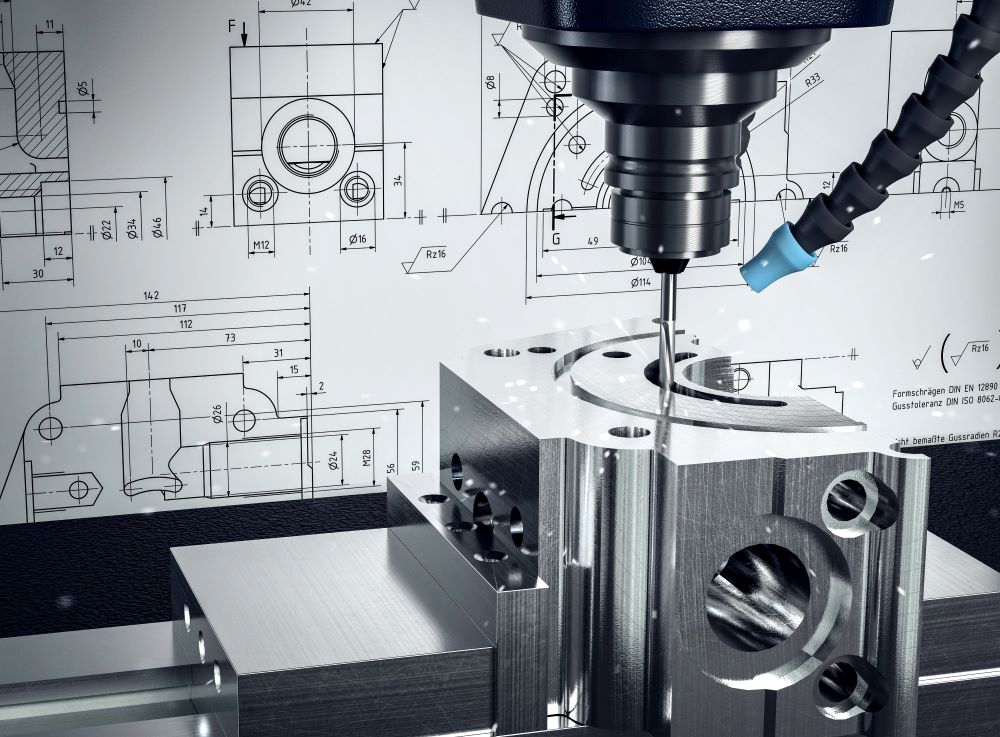
Along with CNC machining, various other accuracy techniques like grinding, turning, milling, and exploration play important roles in bolt manufacturing. Grinding helps achieve great surface coatings and limited dimensional resistances, while turning his explanation is typically used to create their website round parts with specific sizes. Milling and boring procedures are crucial for forming and producing holes in fasteners, guaranteeing they meet exact requirements and function correctly.
Enhancing Speed and Efficiency
To enhance bolt production procedures, it is vital to simplify procedures and carry out efficient strategies that match accuracy machining techniques. Automated systems can deal with repeated tasks with accuracy and speed, enabling employees to concentrate on more facility and value-added activities. By combining these approaches, makers can accomplish an equilibrium in between speed and precision, eventually boosting their affordable edge in the bolt market.
Quality Assurance Actions
Implementing rigorous quality control actions is important in guaranteeing the dependability and uniformity of bolt items in the production process. Quality control procedures encompass different phases, beginning with the selection of resources to the last assessment of the ended up fasteners. One essential aspect of quality assurance is carrying out complete material inspections to validate conformity with specifications. This involves assessing variables such as material strength, composition, and resilience to guarantee that the bolts meet industry standards. Furthermore, monitoring the machining processes is important to copyright dimensional accuracy and surface area coating quality. Utilizing innovative technology, such as computerized examination systems and accuracy measuring tools, can enhance the accuracy and effectiveness of quality assurance procedures.
Normal calibration of equipment and machinery is necessary to preserve uniformity in production and ensure that bolts meet the required resistances. Implementing rigorous procedures for identifying and resolving defects or non-conformities is essential in stopping substandard items from entering the market. By developing a detailed quality control framework, suppliers can support the credibility of their brand and provide bolts that meet the highest criteria of efficiency and toughness.
Verdict
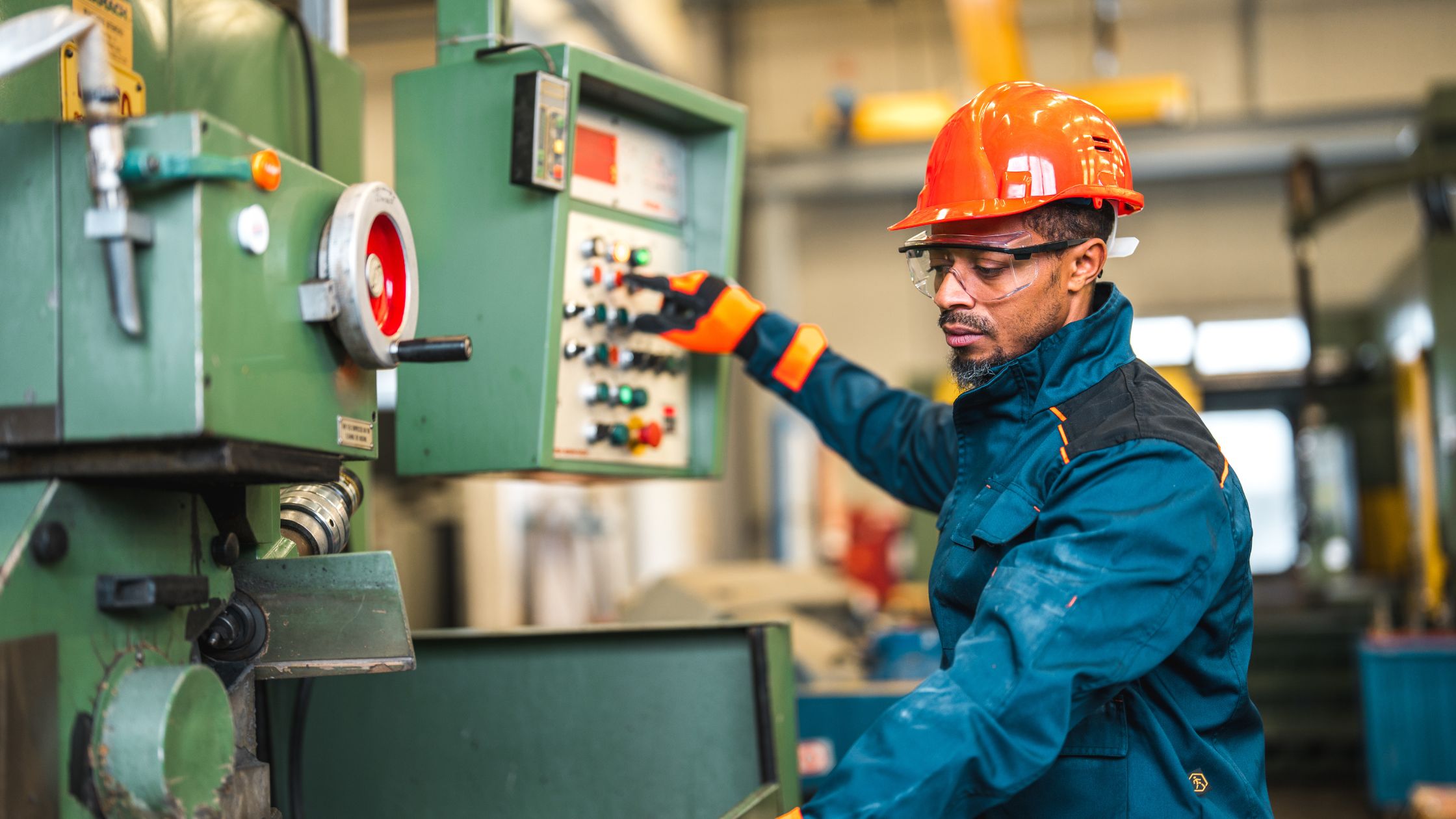
In the elaborate realm of bolts and machining, the pursuit for next page precision and speed is a perpetual challenge that demands careful focus to information and critical planning. When it comes to bolts and machining applications, the product selection plays a vital duty in determining the total strength, durability, deterioration resistance, and compatibility with the intended environment. Accuracy machining involves numerous advanced approaches that make sure the limited tolerances and requirements needed for fasteners.In addition to CNC machining, other precision methods like grinding, transforming, milling, and exploration play essential functions in bolt production.To maximize bolt production procedures, it is important to enhance operations and carry out efficient approaches that match accuracy machining strategies.